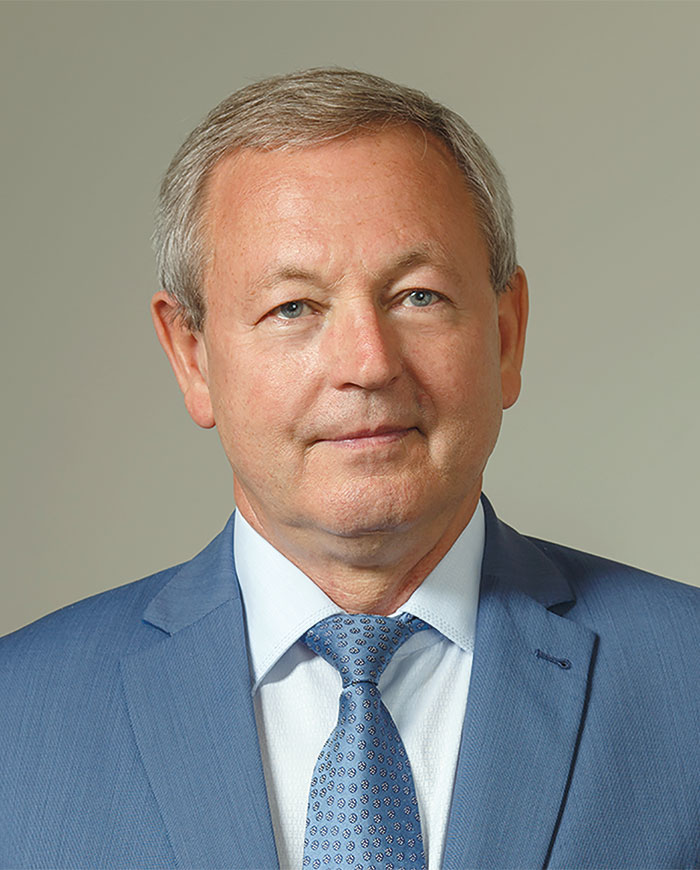
Boris Bogush
Member of the Management Board, First Deputy
General Director-Chief Engineer
– One of the key words in RusHydro’s Strategy is “reliability”. What does it imply?
– We have lived through the tragedy at Sayano-Shushenskaya HPP. Such events cannot be forgotten, both we and the public are very concerned with the reliability of our facilities, whether people can live safely at the downstream side of our facilities, to work at our plants. This is why reliability is fundamental and vital for our company.
Reliability is a complex concept: it includes equipment readiness to bear the load, and keeping permitted wear levels of the equipment, and continuous monitoring of violations of technology . Of course, age of the facilities is important. We have some quite “mature” facilities that were designed according to the GOELRO Plan* – Baksanskaya HPP, Gizeldonskaya HPP. Uglichskaya HPP was built before the Great Patriotic War, the first hydraulic unit of Rybinskaya HPP was put into operation in autumn 1941 (its startup facilitated Moscow survival in the conditions of limited power supply of the wartime).
The company also has new facilities, the construction of which has been completed just recently: Boguchanskaya HPP, Bureyskaya HPP, Gotsalinskaya HPP. They also require heightened attention as there were applied new technology and engineering solutions that have not yet proved their reliability by the test of decades.
We must keep sufficient reliability level at the facilities of any age, of any prehistory. In the conditions of limited financing it is vitally important to correlate reasonably the investment in facilities and required target condition, when the risks become understandable and manageable.
Moreover, the reliability factor includes facilities environmental safety. We must minimize negative influence inherent on any huge structures and, if possible, to reduce environmental risks, including the risks at the big rivers –Volga, Yenisei, Angara.
– How can reliability be ensured in practice?
– In 2012 we launched large-scale and ambitious Integrated Modernization Program (IMP) for the term until 2025. Now we are talking about shifting of completion term beyond 2025 due to the company financing reduction because of critical situation in the economy. We had to review very carefully the investment priorities in guaranteeing of facilities reliability, and their ranking to avoid deterioration of the assets condition. I consider vitally important that even in the conditions of modernization slowdown we manage to keep positive dynamics of our assets reliability improving.
In addition to the Integrated Modernization Program fulfillment, guaranteeing of reliability and safety includes a number of technical measures. The first is continuous improvement of the corporate standardization system in the field of technical regulation. The second is functioning of the safety and reliability management system for hydropower facilities and power-generating equipment of the company. The Analytical Center on the basis of affiliated Scientific Research Institutes as a supporting system for decision-making for the operation of facilities plays key role in it. The Center is a network structure collecting all data from our facilities in online mode analyzing it, checking for compliance with regulations and standards, and issuing recommendations for keeping our assets at the required safety level. The third is implementation of the program of repairs, maintenance, technical reabilitation and modernization (within the IMP scope) with participation of our subsidiary repair and service company having all the required competencies.
– Will all kinds of financial optimization influence the quality of the IMP fulfillment and, in the end, at its reliability?
– We considered such risk. We had to set priorities very carefully of what we are going to do with our funds to avoid it. That’s why even in conditions of certain reduction of financing, equipment condition and our assets condition generally shouldn’t deteriorate in the foreseeable future. The analytics and technical condition index calculation confirm it.
– It is often spoken at the country level about import substitution recently.
– We must presume that significant part of our company equipment needs must be satisfied by the national manufacturers, the share of which will be increasing. Even now imported deliveries of equipment and spare parts are gradually substituted. At the number of big plants there were concluded contracts for equipment delivery where the suppliers are only native manufacturers, our old and reliable business partners. But this process doesn’t mean refusing from cooperation with foreign countries of application of modern technologies developed also abroad.
We are making actual steps towards the localization of equipment manufacture meeting our requirements. For example, large-scale production project on hydroturbines replacement at Saratovskaya HPP is fulfilled by us together with Voith Hydro. This joint venture will manufacture high-quality products of the Russian origin created applying the knowledge of our Austrian partners.